Build-up preparation and pressing
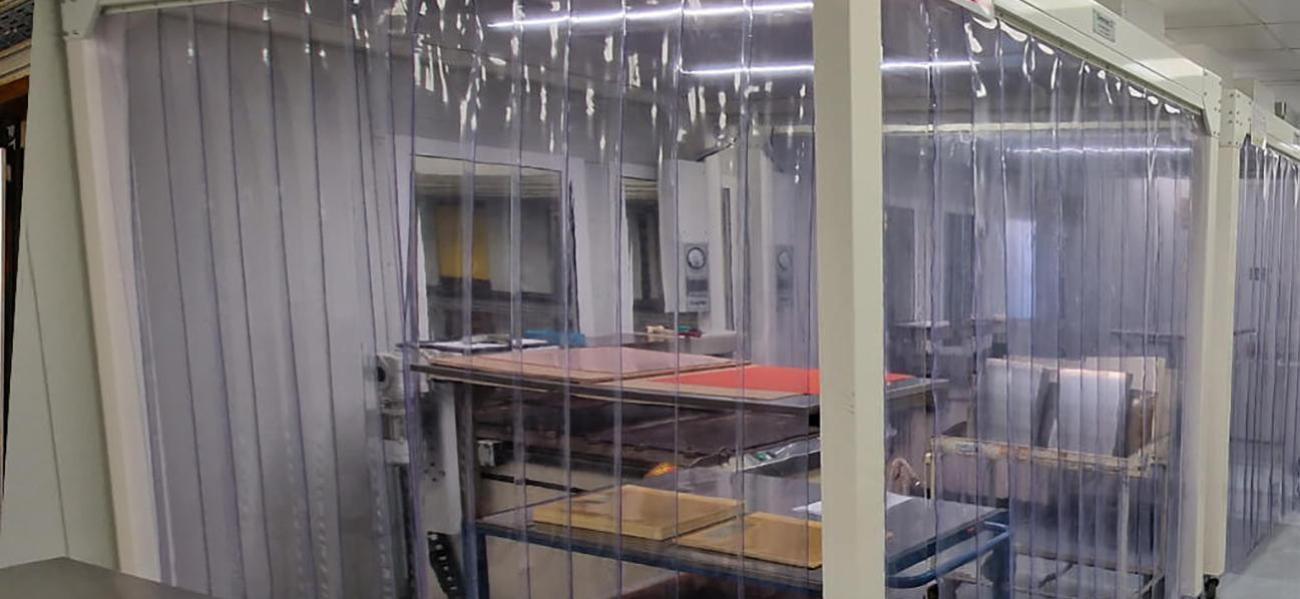
Are you still there?
Come on board with us to proceed with our trip to understand the manufacturing process for the realization of a multilayer printed circuit board.
We are now just after the “black-oxide” process, we have in our hands all necessary inner layers already punched, “black-oxided” and dried, so ready to be staked and pressed together with pre-preg plies to get out of the pressing phase a robust panel, the base of what will become one or more finished printed circuit boards.
Pre-preg is one of the most important materials to produce printed circuit boards, together with inner layers and copper foils.
Il pre-preg rappresenta la "colla" necessaria per tenere insieme, e isolare l'uno dall'altro, i diversi strati interni e i due strati esterni inclusi nello stake-up. Uno strato di pre-preg è di fatto un "foglio" costituito da un tessuto in fibra di vetro pre-impregnato con resina termoindurente, dello stesso tipo di resina di ogni strato interno adiacente.
Pre-preg represents the “glue” necessary to keep together, and to insulate from each other, the different inner layers and the two external outer layers included in the stake-up. A pre-preg ply is in fact a “sheet” consisting of a glass fiber fabric pre-impregnated with thermosetting resin, the same type of resin as each inner layer adjacent to it.
Pre-preg is generally FR4, “flame retardant 4” material, however, as we already explained for inner layers, the type of resin and the glass fibers could have different characteristics giving each PCB mechanical and electrical properties suitable for each specific application.
In order to do the right choice of your supplier for PCBs is important to assure that the PCB manufacturer is capable to work with a consistent range of materials so to assist you properly whatever is the specific application of your PCB.
Consider that different materials could expand or shrink with a different rate with temperature, and this could cause mis-registration between inner layers and delamination of the copper-to-substrate interfaces.
For this reason, to press different materials or, even more, to press mixed materials, is necessary to validate and then to adopt specific temperature-pressure cycles.
To choose the right temperature-pressure cycle for PCB pressing, that also means to choose the speed rate to reach the maximum values of temperature and pressure and the period of time in which it is necessary to keep these values stable once reached, is a very critical matter.
Each resin system – so the resin included in inner layers and pre-preg sheets – has in fact its own glass transition temperature (Tg) that is the temperature at which a polymeric system become an amorphous-viscous material, like a molten glass.
At Tg temperature, in fact, the polymeric chains acquire the “freedom” to move: the resin of inner layers can stick and combine with the resin of which pre-preg sheets are made and with the copper left on top of inner layers after etching so to generate a bulk.
Also consider that different pre-preg have different content of resin and that different resin systems have different capabilities to "flow" as soon as Tg has been reached. Therefore, pre-preg resin % and its capability to flow is another important parameter to control to guarantee an ideal coupling with inner layers given that, on one side, copper percentage – the percentage of copper still on inner layers after etching – could widely vary on the basis of the PCB design and that, on the other side, it is important to avoid the resin to reach and to glue some portions of the PCBs, like the flex layers in rigid-flex PCBs.
Furthermore, pre-preg must be sharply defined for PCBs with “impedance nets” where the combination of thickness of insulation and size of nets determine the impedance values.
Nevertheless, it is important to know that the pressing phase is performed under vacuum conditions: this is necessary to avoid gaps, the so said “voids”, in the PCBs that, later, during the reflow in SMT assembly phase, could be responsible of delamination.
It is now clear that during the lamination process is important to manage some fundamental parameters:
- temperature rise, both for heating and for cooling,
- pressure rise, single or multiple steps,
- vacuum values,
- time needed for each step of the pressing phase.
All these values need to be recorded for a correct process control and traceability.
Last, but not least, to produce reliable printed circuit boards it is necessary to guarantee extreme cleanliness conditions. This is the reason why in build-up area is necessary to use procedures, tools and specific systems for air filtration and treatment so to avoid risks of contamination by “foreign objecyts”.